This current year has been a real pain. However, if there is a silver lining, at least it will give us Generation Z folk stories to tell our future kids. The year 2020 is one for history books all right! We’ve dealt with the lockdowns due to a pandemic, Kobe’s death, and one of the most controversial elections of all time, all jammed into the span of a single year. With quarantine becoming such a major part of day to day life, the use of electronics has depressingly skyrocketed. All the extra home time has meant increased time on streaming services, computer use, and in order to connect with loved ones or work associates: phones, tablets, and laptops. While being bad for your eyes, at least electricity and electronics companies are happy. The virus led to a drastic need for access to the internet and that has meant more time and money is being spent with chargers in outlets. It really is a vicious cycle for your wallet.
My mother is actually the inspiration for what will be this “teardown” of chargers specifically Apple’s iPhone charger. She has made a point to limit how many times I can charge my devices (phone and tablet). While I get the desire to limit the electric bill, I also feel she should recognize the need for technology in such trying times. There is a silver lining here however, the nagging has given me drive to try and answer what and where Apple chargers come from. Well, regular consumers can always head down to their local Apple store, Best Buy, and to the one or two RadioShacks still in existence to go and buy a charger. That is too simple though, where exactly does Apple source their parts and how do they come together into the final product that is essential to the use of our gadgets?. It isn’t an easy question to answer by any means because most companies don’t openly list their sources. This can be for multiple reasons, some more shady than others. Sometimes companies opt to not disclose the information for fear of backlash due to the immorality of certain products and more specifically the way they are processed, they may also avoid it out of laziness and in an attempt to save some cash, another reason is because of the difficulty of tracking these components such as mineral which can come from many different mines. Below is what I was able to dig up and credit is given as all links are sourced as well.
I guess the easiest question to answer is where we should start: what materials or ingredients are needed to make an Apple charger? Well, thanks to reverse engineering, people have taken chargers apart and essentially directed them to work backwards in an attempt to understand how they work. These efforts alongside Apple’s own descriptions have given the general public a list of raw materials that end up composing the 5W USB power adapter specifically. For starters the outer casing (white) is made of a polycarbonate plastic. The circuit-board utilizes epoxy resin (for waterproofing purposes), fiberglass (as a substrate for the circuit), copper, tin, nickel, and gold. The cables are encased copper wires. The resistors are made of tin (tin oxide) and bauxite for alumina. Finally the capacitors are a mix of tantalum and EPDM rubber. So in quick summary, the Apple chargers are a mix of metals and plastic components which are specially formulated to have improved safety which is a plus for consumers but the drawback is the increased price (around 30 dollars).
Let’s take a deeper dive into the small—less than the size of a quarter—yet most complex portion of the charger: the circuit boards. These are composed of plastic and various metals and while Apple does not specify their specific circuit board, the composition can be loosely based on commonly produced printed circuit boards, known as PCBs. The main substrate on which the metals are attached onto is mainly fiberglass epoxy resin. Epoxy resin is useful for maintaining dry circuitry due thereby providing a protective coating. Its production consists of reacting acetone from two phenol groups. Conveniently, acetone and phenol is produced from the cumene process. When cumene is in contact with air, cumene hydroperoxide which ultimately produces acetone and phenol. However, these cumene feed streams usually contain other hydrocarbons since cumene is manufactured from gas feeds. Though most plants aim to reduce emission of these hydrocarbons, leaks can still occur. Assuming this was the same component used for the Apple USB charger, production would imply hydrocarbon emissions as the epoxy resin is derived from the cumene process and it would be worth considering that the charger is potentially causing harm to the environment in this manner.
Shifting focus, the fiberglass component is manufactured from silica sand, limestone, and boric acid. Silica sand is mainly obtained from Wisconsin and Minnesota (main sources for the US), but is also present in large quantities in Australia and Canada according to a US Geological Survey. Mining silica sand involves removal of vegetation, exposing tops of sandstones, excavation, and refilling the area once collection is complete. By doing so, the land usually deteriorates due to loss of top soil, the area experiences an increase in pollution from the rubble and waste from mining, and the ecosystem is disrupted since vegetation is removed. Regarding limestone, the largest source is found in Michigan and is mined through stone quarries, which also impacts the environment by destruction of habitation. However, the degree of impact depends on the location and size of quarry. The other main component of fiberglass is boric acid. US Boric acid is typically industrially produced from borate minerals from sodium borate mineral deposits within the country but Europe imports colemanite from Turkey. In both cases, the raw material is treated with some form of acid to produce boric acid. Put together, silica sand, limestone, boric acid, and other minor components (which vary depending on the manufacturer) are fed into a furnace at temperatures ranging from 1500 to 1700 degrees Celsius.
Additionally, the circuit board contains a mix of metals. There is copper, often found in chalcopyrite and in the US, Canada, Chile, Zambia, and Peru, extracted from foil etched onto the PCB. Mining chalcopyrite involves releasing sulfur dioxide and given the scale, there can be large production of acidic streams and contribution to acidic rain which is harmful to the ecosystem. On top of the copper is a tin-lead coating placed for preventing oxidation. Tin is typically found from cassiterite ore from Bolivia, Southeast Asia, and Nigeria, which is smelted. However, these tin mines require land to be bulldozed and in the process, fertile topsoil is destroyed, leaving acidic soil and inability to develop agriculture in its place. Another metal used in a PCB is nickel which is obtained from sulfide deposits of pyrrhotite or pentlandite found in Ontario or Thompson in Canada. Much like copper and tin, these ores also produce sulfur dioxide with addition of toxic heavy metals. Refining these ores give large emissions of greenhouse gases, with carbon dioxide reaching up to 46 tons per ton of nickel. Another metal present in smaller amounts on the PCB is gold which is mostly mined from Alaska though other places are available such as Australia, Russia, and China. The different methods of mining gold include placer mining, separation by density difference, hydraulic mining, use of water to blast rocks and mercury to pick up gold by amalgamation, and lode mining, digging and excavating with explosives to get further down underground. The latter two methods cause environmental damages by release of toxic compounds or destruction of the ecology. Tin-lead, nickel and gold are then electroplated onto the circuit. Past this, the circuit board is sealed with epoxy, stenciled, and cut. These are then packaged with plastic bags. Based on the components that make up the circuit board of the charger, the environmental impact can be quite severe given that much of it involves mining and release of harmful chemical compounds. Although the PCB is small, Apple mass produces and sells enough of the charger to make an impact.
Another major component of the finished Apple USB charger are the resistors. These provide control of circuit board by reduction of voltage and current. The specific resistor in the charger is a fusible resistor and these are commonly constructed from a ceramic rod wound into a helix. The ceramic rod is made from aluminum oxide, also known as alumina, and is obtained from bauxite ore. The ore is subjected to the Bayer process where it is dissolved in sodium hydroxide solution in which the temperature is changed to precipitate out aluminum hydroxide which is calcined to form the anhydrous oxide. Bauxite is obtained from Africa, Oceania, and South America where bauxite is strip-mined. In the past, there were no actions taken to care for the area designated for the mine but currently there are attempts to return top soil post mine. Forested areas typically are given back 80% of the land but even this causes an ecological change on the species living in the area. The layer of tin oxide is deposited onto the ceramic rod through vacuum deposition. Once the metal is deposited , there is a helical cut into the rod to increase its effective length, thereby increasing resistivity. Once again, the raw materials used for the charger came with negative effects to the environment as was shown with the mining of bauxite.
Capacitors, occupying a large volume of the internal portion of the charger is the next item for life-cycle analysis. The capacitor used in the Apple 5W USB charger contains tantalum, a metal that is paired with Niobium in many alkaline granite-syenite or carbon-atite complexes found in Brazil and Canada. The tantalum ores (tantalite) are mined which are then crushed to release tantalum whereby it is dissolved in acids and extracted with other solvents. The final main part of the capacitor is the rubber used for sealing. This rubber is ethylene propene diene monomer (EPDM for short) and is a polymeric chain. The polymer is manufactured through mixing carbon blacks, obtained from sending crude oil and gas through a furnace, softeners, which is made of paraffinic oils from crude oil, and other various materials. The nature of obtaining crude oil involves drilling which already causes disruption to the environment. Furthermore, the burning of crude oil releases petrochemicals into the air, thereby increasing pollution. This would indicate that by producing the charger, crude oil is needed and therefore producing a causal negative effect on the environment.
Returning to the simplest parts of the charger, the prongs and plastic casings wrap up the component analysis of the charger. The metal prongs for the charger could not be specified but once could guess them to be stainless steel due to the color and appearance. The plastic was surmised to be polycarbonate plastic as Apple had released a statement informing the public that they would be using polycarbonates instead of PVC in their main products. There were no explicit statements about replacing the charger with polycarbonate but based on their attempt to become more environmentally friendly, it was assumed to be applicable to the charger. Production of polycarbonate plastics is an energy intensive processes requiring the polymerization reaction of Bisphenol A (BPA) and phosgene. BPA can be obtained from the production of acetone from cumene when reacted with phenol, as stated before. Phosgene comes from reacting chlorine with sodium chloride and carbon monoxide.
The assembly of the Apple 5W USB could be guessed as the least material intensive portion of the life cycle. Although Apple does not reveal the specifics of how the chargers are built, many of the parts that comprise of the unit are standalone. From disassembling the charger, most of the equipment necessary would probably include some form of screwdriver tool and adhesive to bind the parts together. More investigation is required to determine the actual production process as there were no documents or articles explaining how specifically the Apple charger is built or other generic chargers for comparison.
An important aspect of producing the charger is having the ability to ship it. It is known that Apple assembles most of its product external to the US. Foxconn is a company in Taiwan and manages the Zhengzhou facility according to the New York Times. Apple was revealed to have pre-bought airfreight space and transported using various trucks and Russian military transports. Regarding air travel, most planes use avgas which contain kerosene and lead containing transportation fuel. Kerosene is obtained from crude oil which can be sourced from many places and is typically separated out by fractional distillation. It is approximated that aviation emits a quarter ton of carbon dioxide per hour of flight on average. By flying the products from China to the US (and any other location in the world), Apple is contributing to the emission of greenhouse gases, which can thicken the Earth’s atmosphere as residence of carbon dioxide amongst other gases.
For the waste/disposal portion of the life-cycle, the Apple 5W USB charger can generally be recycled along with other electronics. According to Apple’s website on 2013, they had been accepting of faulty USB chargers and ensured customers that they would “ensure that these adapters are disposed of in an environmentally friendly way” (Apple); this USB charger take-back program only lasted until October 2013. Now it can be assumed that the chargers are simply handled with electronic waste, if they are not thrown away. The circuit boards in the chargers are potentially too small to attempt metal recovery. Resistors can be recycled by simply removing their adhesion to the PCB while capacitors typically have a limited amount of time before requiring treatment at an e-waste center.
As shown by the life-cycle analysis, the Apple 5W USB charger is comprised of various parts that would otherwise be unknown to someone who had not given thought to the device. Not only is the design complex but the sources and impacts of the materials that were used to create the charger varied as well. Although the charger itself is small, the impact of its production can greatly affect the environment.
Work Cited
https://www.popsci.com/technology/article/2013-02/who-supplies-apple-all-those-parts-infographic/
https://www.investopedia.com/articles/investing/090315/10-major-companies-tied-apple-supply-chain.asp
https://www.macworld.co.uk/feature/where-are-apple-products-made-3633832/
http://www.righto.com/2012/05/apple-iphone-charger-teardown-quality.html
https://www.ifixit.com/Teardown/Apple+Wall+Charger+Teardown/120511
https://www.righto.com/2014/05/a-look-inside-ipad-chargers-pricey.html
http://www.aluminum.org/industries/production/bauxite
https://www.telegraph.co.uk/technology/2017/04/20/apple-pledges-stop-mining-iphone-materials/
http://www.newsweek.com/2015/02/13/where-apple-gets-tantalum-your-iphone-304351.html
apple 5W usb power adapter
Tin (mining)
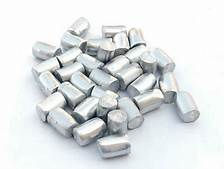
Gold (mining)

Polycarbonate


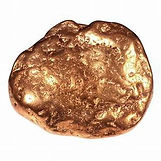

Silver (mining)
Copper (mining)
Epoxy Resin and Epoxy Hardener

Assembly (both human and machine labor)


30 dollar piece of Apple goodness
